Verification and Validation of Actual Measurements and Simulation
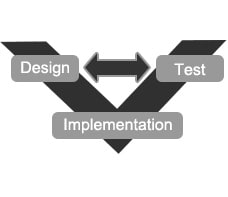
Computer-aided engineering (CAE) analysis, such as structural analysis simulation, is widely used to design and develop transportation equipment. Increasing the accuracy of CAE analysis reproducibility is expected to improve development efficiency, reduce costs, and improve reliability for complex or large structural members that are difficult to evaluate by actual measurement.
In product design and development, there was a time when it was thought that CAE analysis alone could be used to complete the design. Nowadays, it is considered important to perform verification and validation (V&V) by conducting actual measurements under the same conditions as the CAE analysis model and comparing those results with the CAE results in order to confirm the validity of the CAE analysis results. As a result, product design using both actual measurement and CAE analysis has become the norm. Here we introduce examples of improving design reliability by obtaining accurate materials data and examples of V&V.
V&V of GFRP Shear Testing Results
Application
V&V of CFRP Tensile Testing Results
Carbon fiber reinforced plastics (CFRPs) and other composite materials have started to be used to reduce the weight of vehicle bodies in an effort to reduce the environmental impact of automobiles and other transport equipment. Unlike metal materials, the complexity of the internal structure of composite materials is known to result in complex failure behavior that depends on the direction of the primary stress axis, which makes it difficult to establish highly accurate structural analysis models. Here, after a brief overview of composite material characteristics related to CAE analysis, we introduce an example of V&V in which actual measurements and CAE analysis of a thermoplastic CFRP woven material are compared.
Determining the Failure Mechanisms of Composite Materials
—Observation of the Failure Process in CFRTP—
Carbon fiber reinforced thermoplastic (CFRTP) composites, which exhibit excellent processing, mass production, and recycling properties, are expected to replace conventional materials, such as metals, in general-purpose transport vehicles, especially mass-produced vehicles. However, the internal failure mechanisms that occur during the deformation process in CFRTP composites are not sufficiently understood in terms of properties such as static strength and fatigue strength,. Here, we introduce a combined system that enables observation of a load applied to a test sample and internal damage within the sample when the load is applied, key indicators for determining the failure mechanisms of CFRTP composites.
Improving CAE Reliability for Composite Materials
—Three-Point Bending Impact and High-Speed Compression Testing of Composite Materials—
Carbon fiber reinforced thermoplastics (CFRTP) are characterized by their high specific strength and specific stiffness. As a result, they are used in transport vehicles to improve fuel consumption by reducing weight. In the case of automobiles, temperature properties are important because the vehicles are used in cold climates and deserts. Evaluation of the impact characteristics is also important because the material could be subjected to a large instantaneous force in an accident.
Shown here are 3-point impact tests performed on CFRTP samples.
Analysis of the Failure Behavior of Fiber Reinforced Plastics in High-Speed Compression Testing
The static mechanical properties and strain rate dependence of fiber reinforced plastics can vary depending on whether the external force applied to the material is in the tensile or compressive direction. As an example of simulation using compressive properties, we introduce a comparison between the measurement results for a high-speed compression test on a GFRP and the simulation results that take into consideration the structure of the measurement system.
Dynamic Tensile Testing Using a Three-Dimensional DIC Analysis System
—Observation of Strain Distribution and Measurement of Strain in Polypropylene Just before Fatigue Failure—
Previously, it was often difficult to predict the appropriate fatigue life during fatigue testing that applied dynamic test forces or strains at high speeds due to stress concentration in the areas measured with conventional strain measurement methods that use contact-type sensors. In recent years, analysis by digital image correlation (DIC) has attracted attention as a testing technique that can be used to accurately evaluate the static and dynamic mechanical characteristics of materials in the elastic and plastic ranges. The fatigue characteristics of such materials can now be comprehensively evaluated by installing a three-dimensional DIC analysis system in the fatigue and durability testing machine.
Reduction in the Number of Operations for Dimensional Measurement of Complex Molded Products
With a single measurement using a dimensional X-ray CT system, the entire object to be measured can be captured, so the number of measurement operations can be greatly reduced compared to other CMMs.
Improvement of the Accuracy of CAE Analysis of Press Processing of High Tensile Strength Steel Material
The use of high tensile strength steel sheets in automobiles has increased, but the springback phenomenon that occurs in the forming process using metal molds increases the forming cost. It is thought that the accuracy of analysis of the steel sheet springback phenomenon can be improved by applying the Bauschinger effect to the simulation as a material evaluation parameter. In this example, material properties data obtained from uniaxial tensile tests and in-plane reverse loading tests (Bauschinger effect tests) were used to successfully improve the accuracy of simulating press forming of automobile parts with complex shapes, and the rate of agreement for surface accuracy was dramatically improved.