USF-2000A - Features
Ultrasonic Fatigue Testing System
Capable of Testing 1000 MPa Class Steel Material
High stresses can be generated by performing tests at resonance frequencies. With a 20 kHz cycle capacity, this system is able to accelerate fatigue life evaluations of metals and other materials. It is perfect for long service life evaluation of materials or high-speed vibration testing.
20 kHz Vibration Uses Resonance
Extremely Economical with Power Consumption of Only 100 W
The load applied to samples is a 20 kHz longitudinal wave vibration generated by an actuator (Piezoelectric element) and amplified by a booster and horn. Longitudinal waves travel through metals as the metal stretches and compresses in the longitudinal direction. Therefore, a cyclic stress is applied to the metal. The stress is calculated from the displacement of the front edge of the sample, rather than directly measuring the test force using a load cell.
Use of resonance requires only minimal power consumption.
-
Operating Principle of the Ultrasonic Fatigue Testing System
-
-
Testing at Resonance Frequency
-
Standard Layout
For Reducing the Time Required for Fatigue Testing of Metal Materials

With cycle rates up to 20 kHz, the USF-2000 Ultrasonic Fatigue Testing System is able to accelerate fatigue life evaluations of metal materials. This means it can perform tests of 1010 cycles, which would normally take 3.2 years at 100 Hz, in only six days. This exceeds the gigacycle level to achieve ultrahigh efficiency.
Conventionally, it was assumed that fatigue strength of steel was constant beyond 107 cycles. In other words, it was assumed that fatigue failure would not occur at stresses below the fatigue limit for 107 cycles. However, we are now learning that in the case of materials strengthened by quenching or surface treatment, internal inclusions can cause fatigue fractures between 108 and 109 cycles even for stress levels below the 107 fatigue limit.
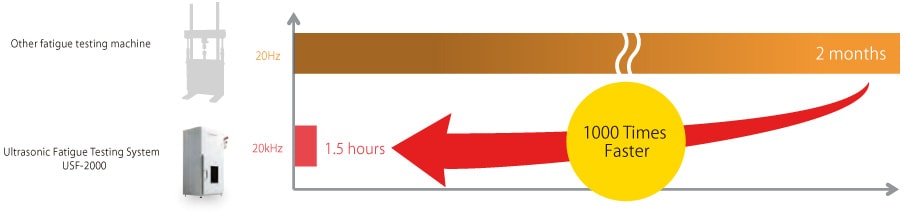
Assume a 108 cycle test is performed at 20 Hz and 20 kHz.
For Analyzing Inclusions in Test Materials
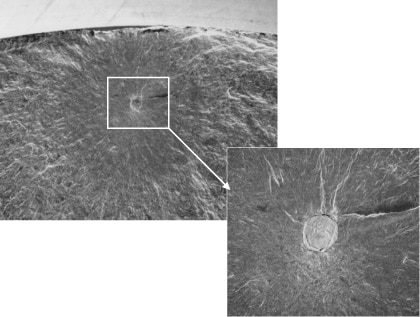
Example of the fatigue fracture surface of high-strength steel fractured by the Shimadzu USF-2000A Ultrasonic Fatigue Testing System
Inclusion where the fatigue fracture originated can be identified
Due to the extremely small size of such defects and inclusions, they are very difficult to identify using non-destructive methods. Typically, materials were sliced and the section surface visually inspected. However, the efficiency of identifying and analyzing inclusions can be increased dramatically by using an ultrasonic fatigue testing machine to the point of fatigue fracture, which ensures a defect or inclusion will be discovered on the fracture surface.
In high-strength steels and other materials, fatigue can propagate from micro defects and inclusions inside the material, which are known to result in fatigue fractures at the gigacycle level. Therefore, identifying and analyzing defects and inclusions in test materials are useful for developing materials with high fatigue strength.