A multifaceted evaluation of plastics - Difference due to PC/ABS blending ratio
A multifaceted evaluation of plastics - Difference due to PC/ABS blending ratio
Difference due to PC/ABS blending ratio
Because PC/ABS is a thermoplastic resin that not only has heat resistance, impact resistance, and flame retardancy as PC characteristics but also moulding processability and plating characteristics as ABS characteristics, it is widely used in automotive interior parts, office equipment and home appliances. By changing the composition ratio of a PC/ABS resin, it is possible to obtain the characteristics that meet the required specifications, but if a mistake occurs in the compounding ratio that is put into the moulding machine, moulding will be defective. For this reason, it is important to confirm the input ratio before moulding, and to evaluate the material properties after moulding to confirm that moulding has been performed according to the purpose. Shown here is an evaluation of the relationship between the sample compounding ratio and various characteristics of a PC/ABS test specimen moulded with different compounding ratios, and an evaluation of the consistency between the compounding ratio and the composition ratio after moulding.
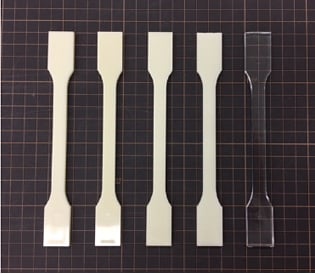
Fig.1 Figure of test specimen
From left, PC : ABS = 0 : 100, 25 : 75, 50 : 50, 75 : 25, 100 : 0
Table1. Heating conditions before moulding
PC:ABS | Kneading with a kneading machine | Kneading with a moulding machine |
---|---|---|
0:100 | Nothing | 220℃,about 250sec. |
25:75 | 260℃,about 120sec. | 260℃,about 250sec. |
50:50 | 260℃,about 120sec. | 260℃,about 250sec. |
75:25 | 260℃,about 120sec. | 260℃,about 250sec. |
100:00 | Nothing | 290℃,about 250sec. |
■ Yellowness measurement : UV-2600i
It was found that the yellowness increased as the ratio of ABS increased.
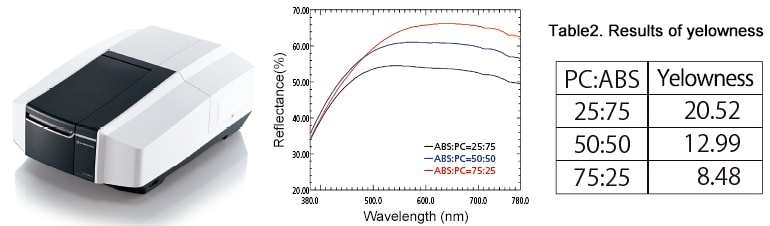
Fig.2 Results of UV
Comparative evaluation of various material properties based on the blending ratio
It is presumed that the material property values (tensile strength, glass transition point of PC) for which linearity was obtained with respect to the blending ratio were not easily affected by effects other than the blending ratio (e.g., thermal deterioration of butadiene in ABS). On the other hand, it is presumed that the material property values (elastic modulus, HIT) for which linearity was not obtained with respect to the blending ratio responded sensitively to effects other than the compounding ratio like a sea stripe structure.
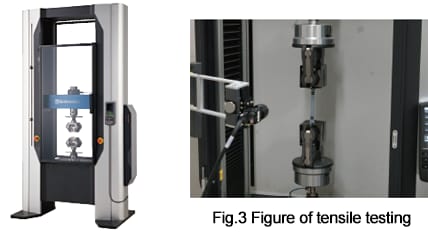
■ Tensile testing : AGX-V
As the blending ratio of the PC increased, the tensile strength increased, and linearity of the tensile strength was obtained with respect to the blending ratio.
The elastic modulus increased from 0:100 to 75:25 for PC:ABS and decreased for 100:0 for PC:ABS.
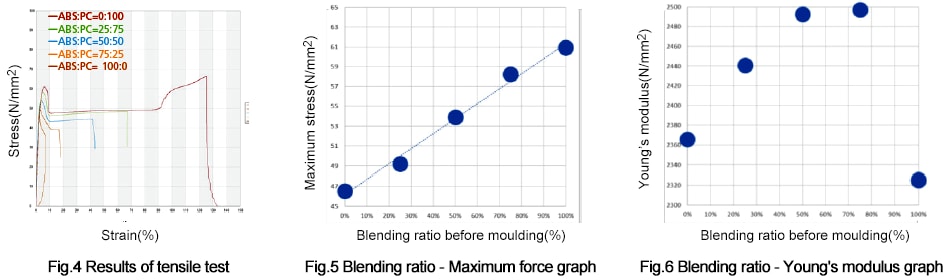
■ Thermal analysis : DSC-60 plus
The linearity of Tg of PC was obtained with respect to the blending ratio.
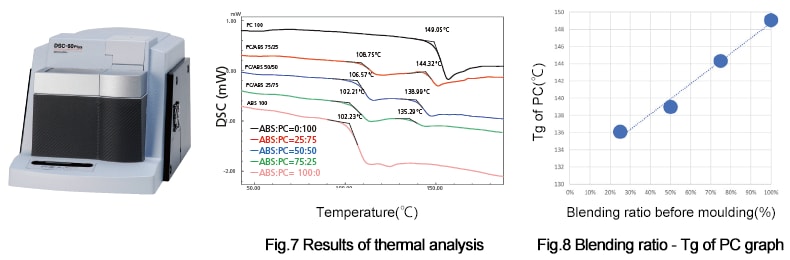
■ Dynamic Ultra Micro Hardness Tester : DUH-210
HIT increased from 0:100 to 75:25 of PC:ABS but decreased at 100:0 of PC:ABS.
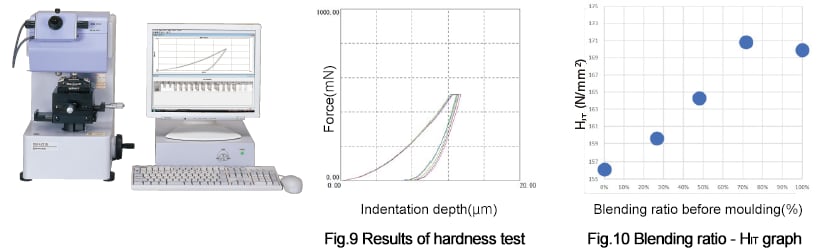
Comparison of the blending ratio before moulding and the composition ratio after moulding Linearity was obtained between the blending ratio before moulding and the composition ratio after moulding.
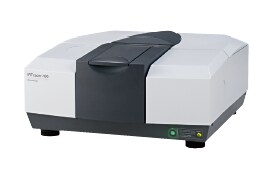
■ Composition analysis : IRTracer-100
Linearity was obtained by the peak strength of the C=O bond and the blending ratio before moulding.
Since the C=O bond is a functional group only for PC, the peak intensity of the C=O bond was converted into the composition ratio after moulding.

Correlation between the composition ratio after moulding and material properties Linearity was obtained in the composition ratio after moulding and material properties. The composition ratio obtained by FTIR and the material properties were compared.
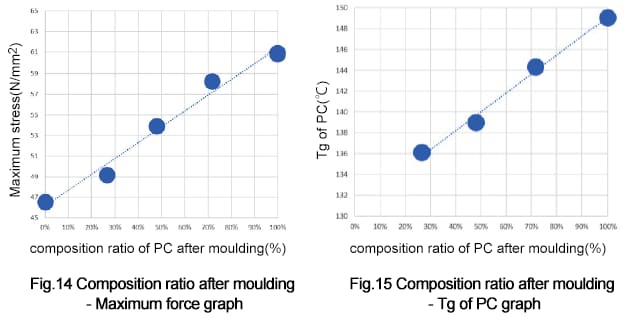
Key points!
- When confirming the blending ratio of unknown materials, it is useful to obtain data for pre-known blending ratio test specimens using evaluation methods which have linearity with respect to the blending ratio, such as tensile strength, Tg of PC, and peak strength of C=O bond.
- Changes in specific material properties do not always indicate changes due to the blending ratio before moulding. Checking the composition ratio with only one material property may lead to misjudgment.
A multi-faceted evaluation helps reduce the risk of misjudgment compared to a single evaluation.