5-4) Vacuum Degassing Using a Gas-Liquid Separation Membrane
Degassing Methods
Vacuum Degassing Using a Gas-Liquid Separation Membrane
This type of Degassing Unit is installed between the mobile phase bottle and solvent delivery pump and is so widely used that it is commonly called a Degassing Unit. These Degassing Units maintain a vacuum pressure on the outside of a resin membrane tube and utilize the permeability of the membrane to remove smaller molecules, such as oxygen and nitrogen, from the mobile phase solution. Because they are able to remove about 70 to 95 % of the air, they are able to prevent problems with bubble formation in flow lines, even for gradients, and they are suited to certain high-sensitivity detection methods.
Procedure
Connect the Degassing Unit to the mobile phase bottle and delivery pump. Drain about 2 to 3 times the capacity of the resin membrane tube (about 15 mL per line for models DGU-3A/4A, 10 mL for models DGU-12A/14A, or 2 mL for models DGU-12AM/14AM) via the pump drain. Alternatively, intentionally aspirate bubbles with a suction filter raised above the liquid surface for about 5 seconds as the effluent is drained, and wait for bubbles to drain out. After bubbles stop draining, continue draining about 10 mL, and then complete the mobile phase replacement.
Advantages
- No restrictions on the mobile phase bottle shape or stopper (other online degassing methods have restrictions).
- The composition of mobile phase mixtures are less likely to change.
- Operating cost is low.
- Handling is easy.
Disadvantages
- Degassing capacity depends on flowrate.*1
- Degassing capacity varies when switching the vacuum pump ON or OFF.*2
*1: Degassing capacity decreases the higher the flowrate. Therefore, if a 100 % methanol mobile phase is monitored at 210 nm, absorbance increases when the flowrate is increased (Figure 23, using models DGU-3A/4A). During water/methanol high-pressure linear gradient analysis, the change in baseline absorbance is a curved line (Figure 24).
*2: There are three types of Degassing Units - (1) models with vacuum pumps that rotate at a constant rpm, (2) models with vacuum pumps that shut off when the vacuum level inside the vacuum chamber reaches a certain level, then automatically restart when the vacuum level decreases again, and (3) models with vacuum pumps that switch ON and OFF at short fixed intervals. Type (1) models take an extremely long time to stabilize and not too many are being sold. Until now, many models were type (2) (DGU-3A/4A). In some cases, type (2) Degassing Units can cause undulations in baselines at 210 nm for methanol UV detection or 254 nm for THF refractometer detection (Figure 25). In more recent years, type (3) models (DGU-12A/14A) have appeared which cause much lower undulation. For refractometers, undulations can sometimes be reduced by connecting the multiple flow lines from the Degassing Unit in series (Figure 26).
Applications
- High-precision (reproducibility of retention times) analysis using low-pressure or high-pressure gradient mixing
- High-sensitivity analysis using fluorescence detection, electric conductivity detection, or electrochemical detection
- High-sensitivity analysis using UV detection. However, this method is not suitable if using mobile phases where fluctuations in dissolved oxygen levels significantly affect the absorbance.
- Normal-sensitivity analysis using refractometer detection.
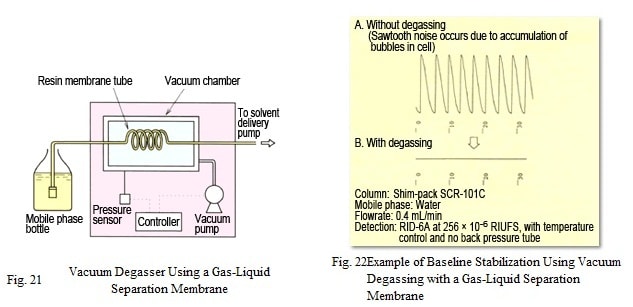
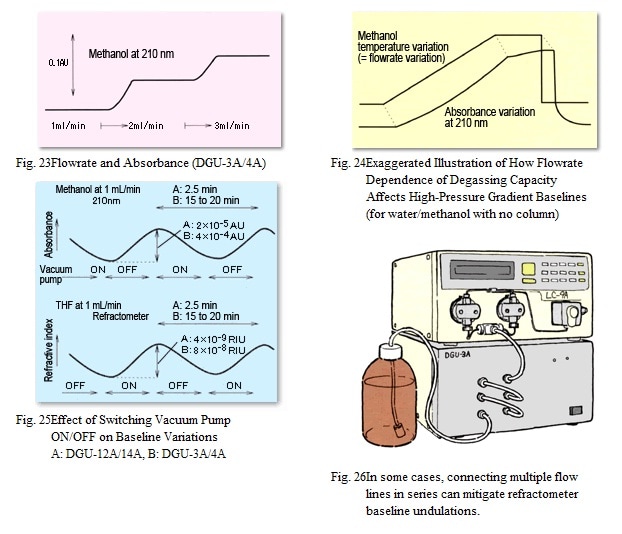
Note: |
This page is a partially revised html version of LCtalk Special Issue 5 (1991). |