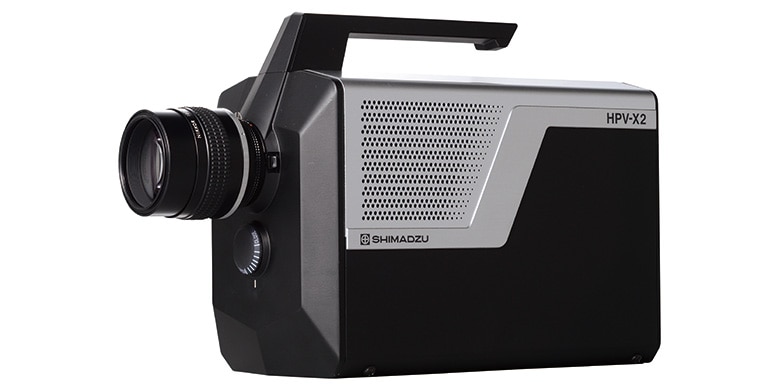
Hyper Vision HPV-X2
INDUSTRY
Engineering Materials, Small Molecule Pharmaceutical
KEYWORD
INTRODUCTION SERVICE&PRODUCTS
Hyper Vision HPV-X2
Predicting the lifespan of an aircraft is important, but composite structures have complex interacting failure modes. As a result, analysis has always been considered difficult. Furthermore, the fracture process of the advanced composite materials used in aircraft is complicated, making it even more difficult to predict lifespan.
Professor Andrew Makeev, introduced in this interview, has been engaged in research in this area since the establishment of the Advanced Materials and Structures Lab (AMSL) at the University of Texas Arlington. He recently produced a number of significant results in collaborative research with aerospace companies concerning the structural analysis and mechanical properties of composite materials. In addition to working on the prediction of lifespan, he is working toward the development of advanced composite materials. Shimadzu's high-speed tensile testing machines (HITS) and high-speed video cameras (HPV) are used for the research. In order to visualize the process of high-speed impacts of composite materials, two of our high-speed video cameras are used in the 3D-DIC (3D Digital Image Correlation) method.
Professor Andrew Makeev
Mechanical & Aerospace Engineering,
*Affiliates and titles of the interviewee are current as of the time of reporting.
University of Texas Arlington
URL
https://www.uta.edu/mae/AMSL
Could you please introduce a little bit of your research and role within the Advanced Materials and Structures Lab UTA?
I am a Professor in the Department of Mechanical and Aerospace Engineering and the Director of the Advanced Materials and Structures Lab (AMSL – http://www.uta.edu/mae/AMSL) at the University of Texas Arlington (UTA). AMSL, established in 2011, has become a very successful model for partnership with government and industry to address most pressing needs and long-range concerns in materials and structures especially for rotorcraft applications. AMSL has been conducting pioneering theoretical and experimental work sponsored by the US Army, Navy, Air Force, and Aerospace Industry, including integration of design and manufacturing processes to improve performance of composites, advanced material technologies, material characterization, structural diagnostics, and prognostics. Our recent research accomplishments are documented in more than 20 articles in the top refereed journals in the field; and recognized by five "best paper" awards at national and international conferences including the Cheeseman Award at the 36th European Rotorcraft Forum (the first and only time awarded to authors based in the United States); 2013, 2014, and 2016 American Helicopter Society Forum best papers in structures and materials; and the American Society for Composites best paper award in 2013. A grant, Integration of Design and Manufacturing Processes to Improve Performance of Composites, awarded to AMSL by the Office of Naval Research (ONR), resulted in breakthrough technology highlighted in "Composite Structures, A View from Inside," in the ONR Innovation Newsletter, Breakthrough Technologies, in 2013. We are currently in the process of transitioning results of our work to accelerate building and qualifying stronger and more durable materials for aircraft, to aerospace industry.
Can you please talk more about the ONR Project? We learnt that your AMSL researchers are researching in collaboration with Bell Helicopter Textron under the ONR project. Why we are asking is because that we have to make sure that our project will not be used relevant to army or be used for development of weapons of mass destruction.
As a university research lab doing fundamental research, our work is not related to weapons development. The results of our research, sponsored by the US Government, are available in public domain in the form of refereed journal publications and conference proceedings. In particular, the ONR Project, Integration of Design and Manufacturing Processes to Improve Performance of Composites, has improved our understanding of the effects of manufacturing defects on strength and durability of composites. Fundamental methods developed under this effort are driven by digital image correlation (DIC) and computed tomography (CT) data to capture physics of the investigated phenomena.
What do think about the difficult points while testing composite materials comparing with conventional materials?
Anisotropic nature and complexity of the deformation and failure mechanisms; and strong susceptibility to variations in manufacturing processes, compared to conventional materials. The effects of manufacturing irregularities or defects on residual strength and remaining useful life of composite structures are not well understood and can be significant. As listed in our recent paper, Analysis Methods Improving Confidence in Material Qualification for Laminated Composites, published in the proceedings of the American Helicopter Society (pdf is also available at http://www.uta.edu/mae/AMSL Selected Recent Publications) "A major challenge, delaying the implementation of recently developed higher-performance materials that offer improved mechanical strength and stiffness at a lower weight, is the lack of efficient common material qualification. The current standard practices are too costly and time-consuming. Due to low confidence in material allowables, the entire material qualification process, including numerous test methods and large test matrices, must be repeated for every seemingly minute change in the composite system." Our work based on advanced measurement techniques including DIC and CT has been essential for improving confidence in material qualification for laminated composites as we are able to measure all key material properties including those which are not typically measured but assumed without verification.
An article, Material World, http://www.uta.edu/inquiry/spring16/features/material-world.php, has been released in the Spring 2016 by the UTA Research Magazine. It has a section, Predicting and Preventing Defects, showing what it oftentimes takes to overcome difficulties of testing composites. In particular, we successfully integrate the following three key elements. First, high-resolution CT based nondestructive subsurface measurement and structural diagnostics enables accurate 3D measurement of defect location and size with automated transition to structural models. The automated data transition ensures the objectivity or independence upon the tester’s level of expertise or interpretation, providing consistent results. Second, accurate and efficient methods based on DIC capture 3D material properties of the composite material using the minimum amount of mechanical testing. Finally, the physical observations and material properties are combined in a computational analysis to capture multiple damage modes and their interaction and predict structural lifetime performance. In 2016, AMSL will also start exploring a fourth element – how to predict where the manufacturing irregularities will actually occur, which could allow industry to control for such defects in the manufacturing process. Developing composite process simulation tools able to predict manufacturing-related defects; and integrating them with our tools for structural diagnostics and performance prediction will be essential for closing the loop on effective control of the manufacturing process to prevent formation of the critical defects and realize the full potential of composites.
We learnt that the AMSL’s most recent equipment acquisitions including a CT from North Star Imaging.
Actually, our North American Subsidiary has begun CT business since last year. We will actively make effort on brand-building and complete service providing including support, maintenance asap in the North American market. We really expecting that we can build deeper collaboration about the Nondestructive inspection.
AMSL has a large start-of-the-art microfocus CT facility from North Star Imaging; and ONR has recently sponsored the development ofinsituscanning ability for this facility including the design and integration of a 11 kip (50 kN) load frame. UTA has also purchased SMX-100CT, and AMSL is committed to at least 50%-time usage of this system. We hope we can make more communication about application in the future.
What is the difference between DIC and traditional imaging measurement?
For the materials and structures purposes including the assessment of stress-strain material properties as well as strength, fatigue, and impact resistance characteristics, DIC full-field measurement technique assesses strain based on quantifying locations of a random texture on specimen surface using stereo images. DIC provides additional flexibility compared to the strain gage-based techniques: strong-gradient strain distributions could be evaluated. DIC enables us to design test methods allowing for measuring multiple material properties in a single experiment and using the same test configurations at various loading rates, i.e. quasi-static, fatigue, and impact conditions. For example, we can quantify all basic material properties for predicting cracks and delaminations in multi-directional laminated composites, using only two DIC based test methods developed at AMSL, relying on simple unidirectional specimens. DIC based methods are robust and they require smaller effort to prepare the test specimens compared to other techniques.
What do you think about advantages of 3D measurement?
3D measurement is the only way to assess the out-of-plane deformation. That is also critical for measuring the in-plane strain components once they exceed the limits of linear elasticity assumptions applicable to small strains. Accurate in-plane strain calculations generally require measuring the out-of-plane displacements.
How many Shimadzu High-speed camera are you using on your research?
We started with two HPV-2A camera based DIC system. We later acquired an HPV-X camera and recently upgraded it to HPV-X2. We are currently in the process of acquiring the second HPV-X2 camera.
What do you think if there is any advantage about HPV-X2 comparing with HPV-2A?
Higher frame rate, higher resolution, light sensitivity, and more images.
Can you please let us know why do you need the Max 10M fps speed of HPV-X2 on your research?
We are only able to do DIC at full camera resolution at the speeds up to 5M fps. Even at low-velocity impact loads we want the highest frame rate ability as we do not want to miss any strain oscillations in the process of capturing the test specimen response to loading.
Sensitivity of HPV-X2 have been upped to 6times than previous model. Have you ever experienced any advantage during using the high sensitive HPX-2?
Yes, strobe-lights become less needed.
Do you think if there is any functions should be added or be improved of the HPV-X2?
Better image pre-processing for DIC analysis to the level currently available for slow-rate cameras. In particular the full capability of the Correlated Solutions VIC-SNAP must be integrated. That not only includes the image acquisition preprocessing functions but also accurate synchronization with the load data from the load frames.
What kind of products or service are you expecting of Shimadzu?
Shimadzu has been making some of the best analytical and measurement equipment on the market. Accordingly I am expecting Shimadzu keeping the highest level of service including support, maintenance, and software and hardware upgrades.
Can you please let us know what kind of impression do you have of Shimadzu?
Shimadzu is an extremely reputable company that UTA and AMSL would like to further extend our relations including collaboration. Perhaps there might be mutually interesting topics for collaboration related to nondestructive inspection of composite structures for manufacturing defects. In particular, AMSL has been successfully working on developing software capability to break through the current object size limitation for x-ray computed tomography. We developed a code that can run and compare different reconstruction algorithms including what is currently used in the industrial CT as well as some promising methods for limited-angle tomography. We are interested in growing collaboration and partnership especially in areas related to DIC and CT data driven modeling and discovery.
Thank you so much for your time today.
Hyper Vision HPV-X2
Professor Andrew Makeev visited Japan for the purpose of confirming the operability of the imaging data using a new system configured with new 3D-DIC software from Correlated Solutions Inc., which is compatible with Shimadzu’s most advanced high-speed video cameras (HPV-X2). This strength evaluation system, currently only realized by Shimadzu, is effective at evaluating composite materials during high-speed impact testing. The aerospace industry, which is based in the USA and Europe, is similar in size to the automobile industry, and Shimadzu intends to continue to proactively propose testing machines and analytical instruments for use in composite material evaluation.